Discover the particles on the ground from Daisy smashing iPhones to get to their elements Daisy is comprised of 4 sections, all housed inside this one construction. (Photograph: TechCrunch, Brian Heater)
Apple has proven off its Daisy robotic for recycling iPhones earlier than, however now it is grow to be a lot quicker through the use of brute pressure.
Daisy has been stripping outdated iPhones for components for a few years now, and is a part of Apple’s goal to finish mining for sources. it was itself an replace to a earlier robotic known as Liam, which might initially dissemble an iPhone in 12 minutes.
Later variations of Liam received that right down to 11 seconds, and in keeping with TechCrunch, Daisy now strips an iPhone in 18 seconds. That is clearly slower than with Liam, however the place the older machine might solely dissemble the iPhone 6, Daisy can deal with 29 totally different fashions.
“One metric ton of fabric recovered from Daisy prevents 2,000 metric tons of mining,” mentioned Sarah Chandler, Vice President of Surroundings and Provide Chain Innovation.
Regardless of the advantages, and despite its radically improved pace, Daisy’s imposing 33-feet of robotics can strip as much as 1.2 million iPhones a yr — whereas an estimated 150 million smartphones had been discarded in 2023. Apple has provided to license its Daisy patents without cost to anybody that desires it, however to this point not one single firm has taken it up.
“I feel we have to proceed to do increasingly with buyer engagement,” says Chandler. |That is why this is not going to be Daisy’s best day… she’s working a little bit slower to accommodate [a facility tour]. However that is value it. That is how we get the message out.”
Brute pressure recycling
Beforehand, Apple’s recycling robots used to grip the iPhone and fairly painstakingly unscrewing and eradicating every part. Now these elements are punched straight out of the system, ripping aside the iPhone for pace.
The method is completed in a collection of 4 phases, beginning with bucketfuls of iPhones being dropped right into a chute. Daisy places every one on a conveyor belt, and makes use of machine studying to find out what particular mannequin it’s.
Subsequent the show is peeled off, and every system is subjected to temperatures of -80 levels Celsius (-112F), which makes adhesive within the batteries fail. Daisy then knocks that battery out, and the iPhone continues to the following phases.
These finish with elements touchdown on a spinning floor, the place a human being will type them. Then boxed-up units of elements are despatched out to e-waste firms.
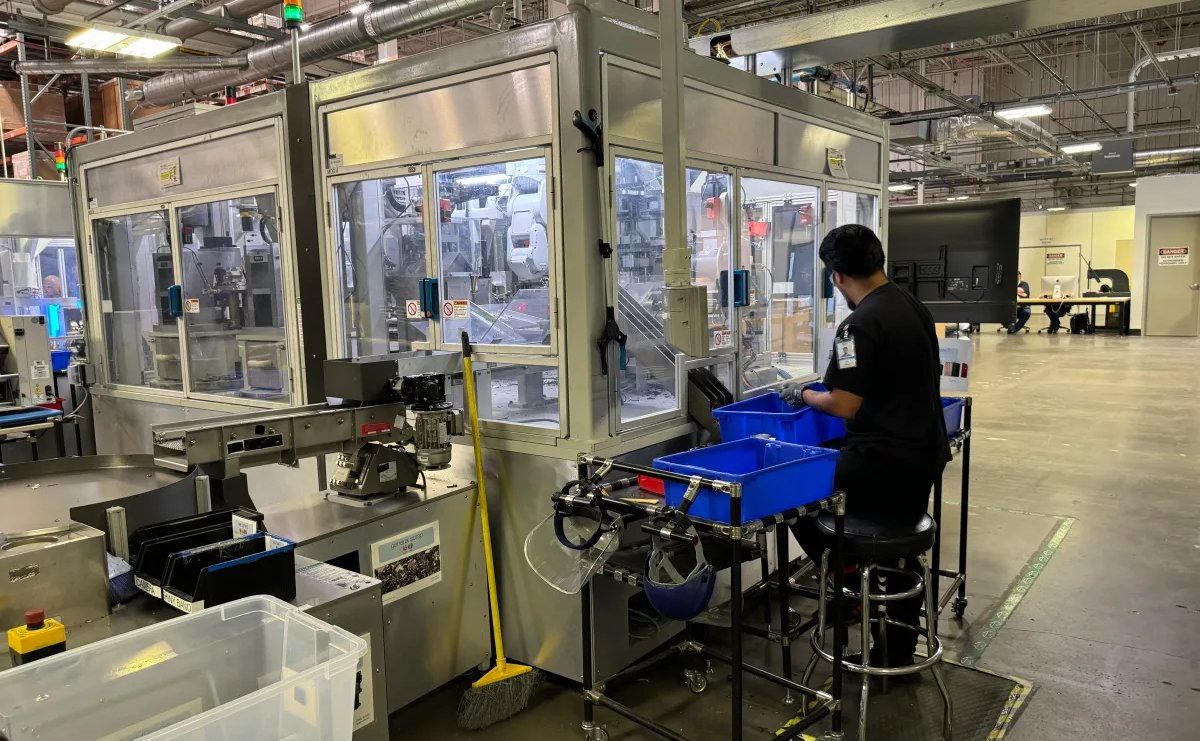
Daisy is comprised of 4 sections, all housed inside this one construction. (Photograph: TechCrunch, Brian Heater)
Recycling in Austin, Texas
Whereas these e-waste corporations are exterior, Apple says that it goals to do as a lot of the recycling in-house as it may possibly.
“It is so vital to do it internally,” says Patrick Wieler, Recycling Innovation Engineer. “Each evolution taught what we are able to do with automation and offers us a giant step ahead.”
“It is a fixed dialogue,” he continues. “We study a ton from the automation workforce engaged on the brand new merchandise, as a result of they’re at all times confronted with their very own distinctive set of challenges.”
“We will construct on their studying there after which vice versa with their groups,” he says. “After we share how we had been programming Daisy, it permits them to consider new approaches to the automation of latest merchandise.”
Apple has two of the Daisy recycling robots, with one based mostly within the Netherlands, and one in Austin. Chandler says being based mostly in Austin has been notably helpful to her workforce.
“We have robust, longstanding connections right here,” she says. “We have clearly received a number of huge campuses right here, so we’re in a position to do a bunch of recycling right here.”
“And it has been nice for educational partnerships, too,” continues Chandler. “We’re in a position to get fairly a couple of interns… we get lots of us who need to discover robotics, recycling and materials restoration.”
Individually, Apple has been increasing its Austin campus, even a it shuts down others together with a San Diego workplace. Some 121 folks from that workplace had been provided roles in Austin.